Aux jumeaux numériques de ses usines, Renault a ajouté la capture et la restitution des données en temps réel. Puis, une plateforme de pilotage de l’ensemble de ces informations et permettant de créer différents cas d’usages à la vue du jour.
Le constructeur automobile travaille à la numérisation de l’ensemble de ses processus, de la formation des salariés à la livraison des véhicules aux clients en passant par l’optimisation des processus de conception et de fabrication. Après quelques années où il s’est concentré sur la structuration de la donnée, le constructeur a pu passer à l’échelle avec la création en interne d’une plateforme reposant sur un standard unique de la donnée. Retour sur la transformation numérique du constructeur Français.
Une solution interne proposée par Atos
Entre 2016 et 2018 ce sont 120 millions d’euros qui ont été investis notamment sur le réseau dans les usines. Puis, entre 2019 et 2021 ce sont 270 millions d’euros qui ont été utilisés pour réaliser des jumeaux numériques des usines et de la chaîne d’approvisionnement, tout en nouant des partenariats avec la start-up française Shippeo pour améliorer la visibilité sur la supply chain ou Google en tant que fournisseur de la plateforme cloud.
Sur cette période de collecte des données, le constructeur automobile explique n’avoir pas trouvé de solution de gestion et de visualisation des données correspondantes à sa demande puisque la plupart des offres concernaient uniquement certains segments. Ou Renault cherchait à avoir une visibilité complète, d’où le développement en interne de cette plateforme.
Les données utilisées ont commencé à être utilisées pendant que la plateforme IDM4.0 a été mise en place entre 2021 et 2022 ainsi que la “central tower” offrant une vision centralisée de l’ensemble des informations. Sur cette période ce sont 390 millions d’euros qui ont été investis par le constructeur. Un salarié qu’explique Renault est alors passé “d’un jumeau numérique statique à une capacité de projection et d’interaction en temps réel”. En parallèle, il s’est également rapproché d’Atos pour monétiser son savoir-faire industriel. La solution est commercialisée depuis juin 2022 sous le nom ID@Scale. Atos assure être en discussions avancées avec 5 clients et avoir signé le premier client dans l’industrie manufacturière.
La plateforme IDM4.0 regroupe quatre dimensions jugées essentielles : la connexion des équipes et des machines, les jumeaux numériques des installations et de la supply chain, la connexion à l’écosystème au-delà des murs des usines, la dimension technologique qui vient s ‘intégrer au-dessus de la donnée.
La connexion des équipes et des machines
Côté chiffres, Renault précise : 8500 équipements sont connectés dans les usines, 600 équipements répartis dans une vingtaine d’usines sont susceptibles de capteurs de vibrations, une soixantaine de procédés industriels sont modélisés (vissage, usinage, soudage, emboutissage, remplissage, etc. ), il y a 4400 Digital Work Station (DWS) ou salariés connectés. Le tout permettant de collecter un milliard de jeux de données par jour.
Par exemple, sur le site de Maubeuge il est possible de visualiser l’ensemble des objets concernant le flux de fabrication des Kangoo : de la visseuse à l’opérateur en poste. Les personnes présentes sur les chaînes de fabrication sont des opérateurs connectés : au début de leur prise de poste ils doivent valider qu’ils sont bien présents, qu’ils récupèrent le poste en bon état, que tous les outils sont là, etc. cas de problème, l’information est remontée directement à l’opérateur senior qui reçoit une alerte et peut régler le problème. En parallèle, le chef d’équipe reçoit la même alerte qui passe au vert lorsque le problème est réglé. “Renault dispose de 4000 tablettes et 3000 chefs d’équipe connectés”glisse une salariée.
L’ensemble d’une ligne de production de Maubeuge est visible.
Au-delà des salariés augmentés, les robots sont bardés de capteurs et remontent de nombreuses données – plus de 70% des équipements industriels sont connectés – qui permettent de détecter de nombreux problèmes. Par exemple, il est possible de savoir lorsqu’une électrode d’un robot de soudure va rester collée. Cela est dû à un désalignement du robot auquel il est facile de transmettre sans avoir à subir un arrêt de la chaîne de production.
L’apport des jumeaux numériques
Renault n’a pas seulement réalisé des jumeaux numériques de ses usines, mais également de sa chaîne d’approvisionnement. Des avatars représentent chaque objet et les différents flux de marchandises peuvent être analysés. A partir de ces jumeaux numériques, le constructeur a également pu mettre au point une quinzaine de formations en réalité virtuelle dont une pour la peinture de la Mégane E-Tech. Le constructeur s’est appuyé sur la maquette 3D développée en interne.
Avec cette formation, le personnel dédié à la peinture peut s’entraîner à avoir le bon geste pour optimiser la consommation de peinture tout en peignant au mieux. Une fois le module de peinture terminé, le logiciel fait un retour pour signaler lorsqu’il y a trop ou pas assez de peinture sur la carrosserie. Renault assure que les personnes ont été formées quatre fois plus vite grâce à la réalité virtuelle. “Le constructeur dispose d’au moins deux casques de réalité virtuelle sur ses 35 sites”précise une responsable de la formation en réalité virtuelle. “Renault a formé 70% de ses peintres en France avec ce dispositif”ajoute-t-elle.
Il est possible de s’entraîner à peindre en réalité virtuelle.
Les jumeaux numériques et les outils de réalité virtuelle sont également utilisés pour étudier comment agencer au mieux les zones de production, valider les conditions ergonomiques de chaque poste de travail et s’assurer que toutes les taches peuvent être réalisées au mieux.
La connexion à l’écosystème extérieur à l’usine
Avec sa plateforme IDM4.0, le constructeur récupère et collecte des informations bien au-delà de ses propres usines. Côté supply chain, l’objectif est de planifier au mieux la production pour maximiser les marges. Pour cela, il est nécessaire d’automatiser la récupération de données auprès des fournisseurs ainsi que celle concernant le transport de marchandises.
Lorsqu’il y a un problème d’approvisionnement, celui-ci est tout de suite signalé afin de revoir le plan de production. Des scénarios de crises sont proposés et l’opérateur peut prendre la décision finale. Renault assure vouloir continuer à développer des algorithmes pour améliorer et approfondir les outils de prédictions et prescriptions sur ces sujets. Allant dans ce sens, un des objectifs est d’optimiser les routes prises par les camions ainsi que leur taux de remplissage ce qui permet de réduire les stocks.
La dimension technologique
Le quatrième élément mis en avant par Renault au sujet de sa plateforme est la dimension technologique qui vient se positionner au-dessus des données. “Des modèles d’intelligence artificielle et de machine learning peuvent venir s’améliorer encore plus les capacités de la plateforme”, déclare un salarié. A ce niveau, le constructeur cherche à tirer profit du cloud et travaille avec Google sur certains sujets.
Renault affirme que sa plateforme facilite le déploiement de modèles d’intelligence artificielle. Par exemple, les opérateurs sont aidés par un système d’intelligence artificielle pour réaliser les contrôles visuels des pneumatiques : “le système propose, prédit ou alerte et l’opérateur décide”, résume un salarié. Le logiciel, développé en partenariat avec la start-up Buawei, détecte les anomalies sur les pneumatiques à l’aide d’images. Que ce soit un pneumatique en mauvais état ou monté du mauvais côté, un problème de conformité des vis ou le fait que deux pneus différents aient été configurés, le logiciel d’alerte du problème détecté.
Une fois qu’une solution de ce type est mise au point sur un site, elle est partagée par le constructeur dans une bibliothèque d’algorithmes pour qu’elle soit reprise par d’autres usines.
Grâce à cette plateforme IDM4.0, Renault souhaite réduire ses coûts, avoir plus de visibilité, améliorer la prévention et l’anticipation, réduire les délais entre les commandes et la livraison, etc. A ce jour, il assure que cette plateforme lui a permis de réaliser 80 millions d’euros d’économie notamment grâce notamment à 300 alertes vibratoires lui évitant l’arrêt de la production, l’amélioration de la qualité du soudage par points, l’inspection visuelle du châssis ou encore le suivi des véhicules du prototype jusqu’à la série. Mais il espère réaliser jusqu’à 320 millions d’euros d’économie d’ici 2025. En attendant, Atos cherche à commercialiser cette solution. Le succès avancé par Renault pourrait-il être reproduit chez d’autres industriels ?
Sélectionné pour vous
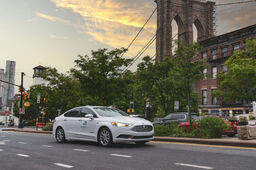